With more demand for productivity, you need to keep up and generate an ROI for any investment you make. As a solution with more functionality and a significant increase in accuracy and efficiency, the Miner Operated Survey System (MOSS) is a total underground solution.
Accuracy and efficiency are two critical elements in the mining industry today. It is crucial that miners follow mine plans accurately to be as efficient as possible. With each meter of advance, there is a chance of overbreak, underbreak, and deviation from the designed mine plan. These three factors can result in a substantial loss in money and time. Overbreak, as well as damaged zone, significantly impacts the project cost, construction period, safety and performance of the underground structures.
The Miner Operated Survey System (MOSS) is an underground surveying software that supports a wide range of Leica robotic total stations, including the latest state-of-the-art MS60 3D face-mapping technology. MOSS integrates mine design specifications and drawings when completing mark-ups, and provides real-time information to miners, engineers and geologists. The software is fully matured and packed with decades of input from miners, geologists and engineers.
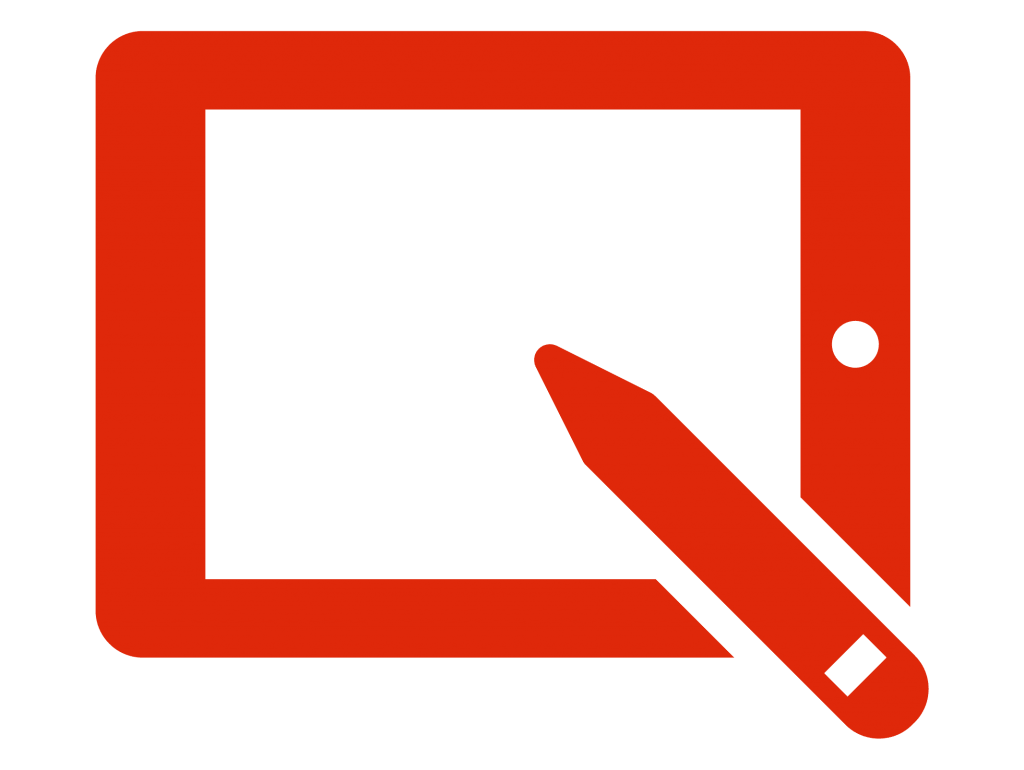
Mine from the Design:
With MOSS, the engineer’s plan for the mine is followed accurately, measuring each face with real-time results, ensuring that the miners can get to the ore as efficiently and accurately as possible.
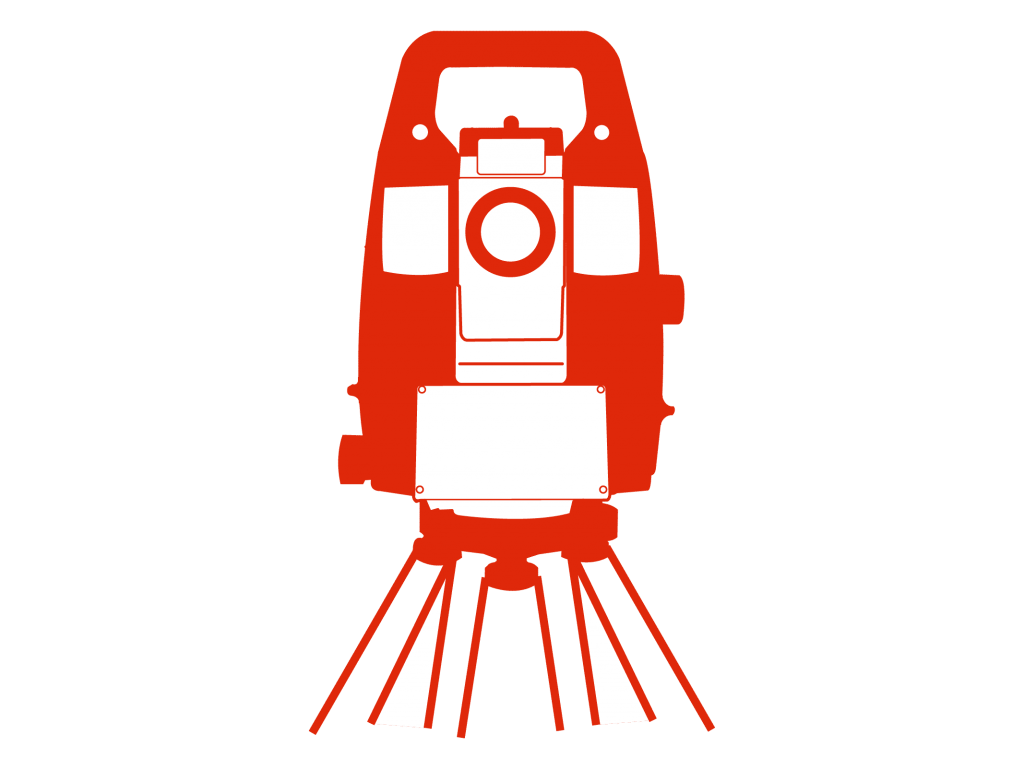
UG Survey at Every Face:
With MOSS implemented in active headings, we see a direct result to improved workflow and faster cycle times. The real-time data MOSS is able to capture and provide solutions for: Comparison between Mine Design and Actual Blast, Setting of Line and Grade, Collar Drill Hole Location, 3D drill Pattern Generator, Face Scanning and Photos, and Cavity Monitoring. The entire seven-step process takes on average twenty to twenty-five minutes.
3D face-mapping technology. MOSS integrates mine design specifications and drawings when completing mark-ups, and provides real-time information to miners, engineers, and geologists. MOSS can reduce overbreak to under 10%, as well as providing very accurate line and grade markups for every round
Our MOSS solution helps to optimize your mine by guiding the miner to accurately mark up the face, calculating the centreline, crank line, and smoke marks for the miner all in just less than 13 minutes! MOSS streamlines the entire process of marking the face for accurate and efficient rounds each time, as well as bringing the data to the surface!
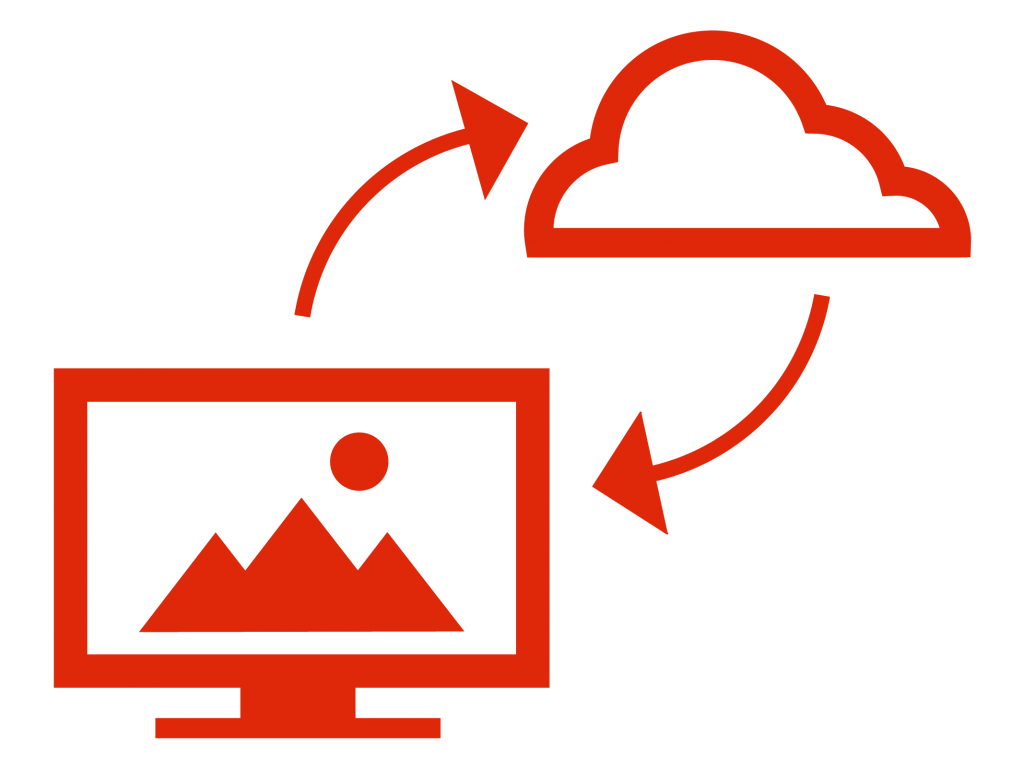
Real-time Information:
MOSS has proven direct cost savings due to the real-time data provided to the miner at the face. Each time the MOSS process is completed, the mine plans are updated, this results in newly updated plans every day. After the tablet is synced, surface workers can quickly see overbreak or underbreak, deviation from mine design, topes, and volumetric data. See an immediate return on investment in direct relation to more accurate metrics to month-end reconciliations and financials.
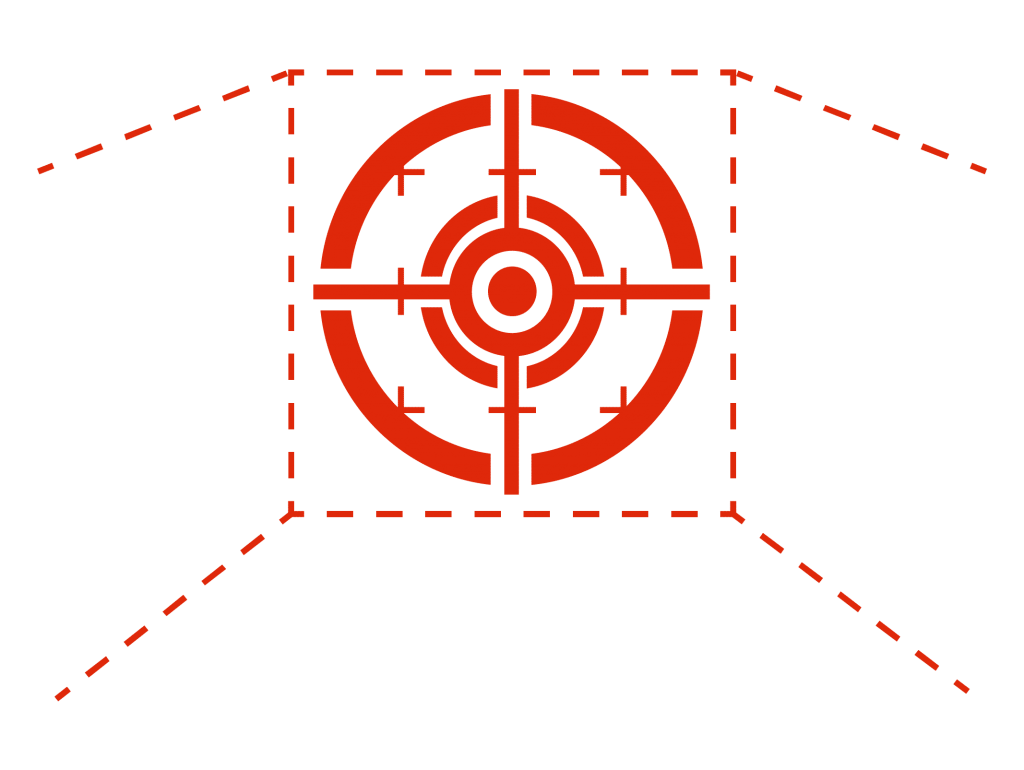
Increased Line & Grade
The MOSS solution helps to optimize your mine by guiding the miner to accurately markup the face, calculating the centreline, crank line and smoke marks for the miner all in just less than 13 minutes. MOSS streamlines the entire process of marking the face for accurate and efficient rounds each time, as well as bringing the data to the surface.
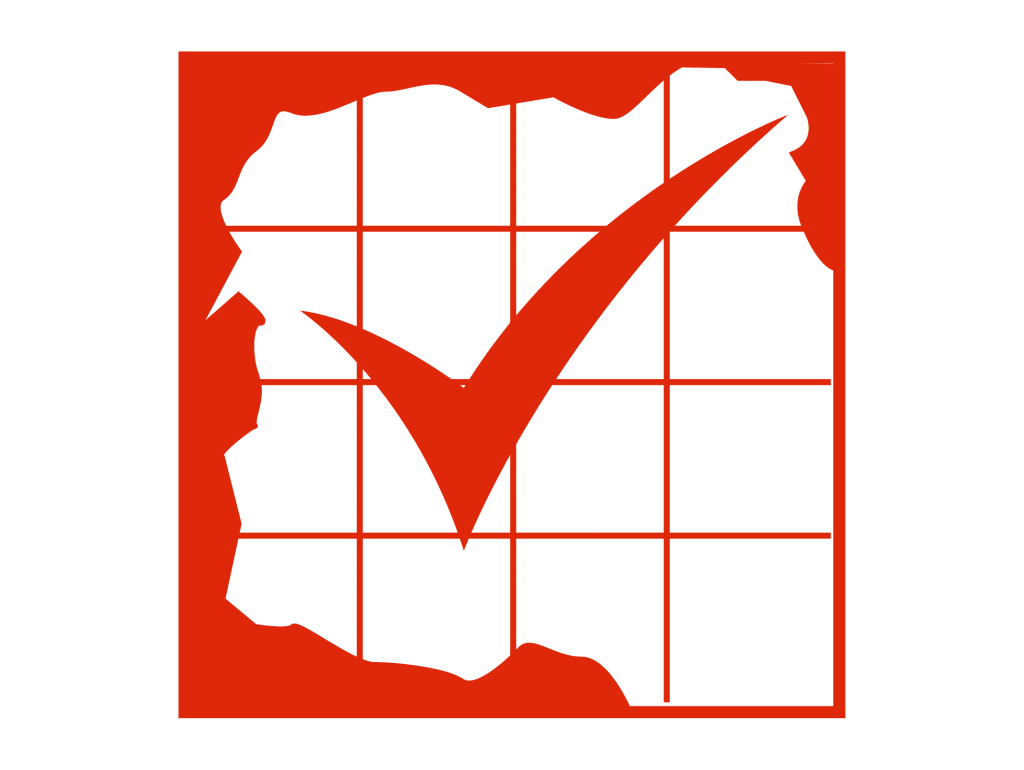
Reduction in Overbreak & Underbreak
“Studies show that most mines are looking at an overbreak of up to 15%.” (Lalonde, 2016). When a mine uses MOSS it drastically reduces overbreak and underbreak – by 10-15%, and takes the guessing out of the process.
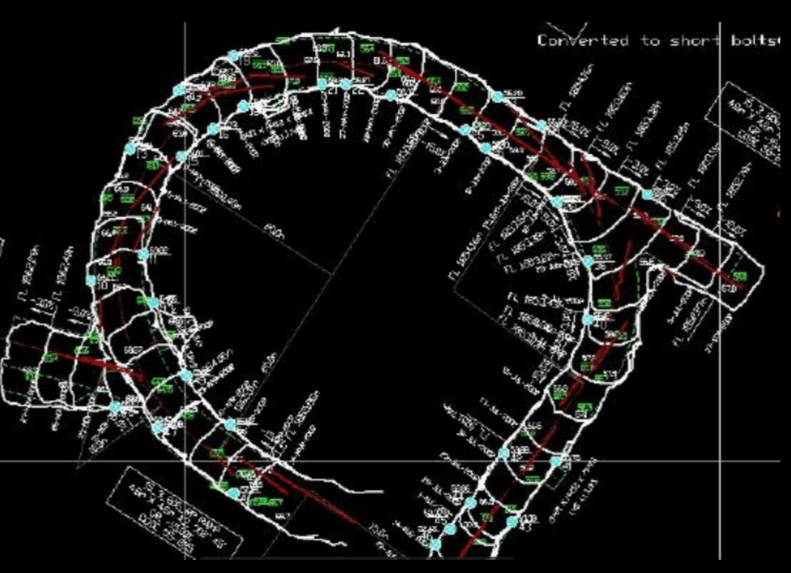
Mine From Design with MOSS
- Overbreak / Underbreak – Reduce by up to 10-15%
- Accuracy for line and grade at every round
- Prevent errors and the need for costly reworks
- Efficiency in the development and production stages
It is crucial that miners follow mine plans accurately to be the most efficient possible. With each meter of advance, there is a chance of overbreak, underbreak, and deviation from the designed mine plan. These three factors can result in a substantial loss in money and time. Over-break, as well as damaged zone, significantly impacts the project cost, construction period, safety and performance of the underground structures.
FAQ
MOSS isn’t just survey equipment
The MOSS system helps the miner to follow mine plans as accurately and efficiently as possible. With each meter of advance, there is a chance for overbreak, underbreak, and deviation from the designed mine plan to occur.
With MOSS mine design specifications and drawings are integrated into the system. When completing mark-ups, real-time information is provided to miners, engineers and geologists, increasing efficiency, and accuracy to the original design. Mine to design with MOSS.
What makes it different from the older methods?
It is crucial that miners follow mine plans accurately to be as efficient as possible. With MOSS, there is less chance for mistakes to occur that could result in a substantial loss in money and time. Even a beginner miner can accurately and efficiently use MOSS and have little overbreak at each face.
Will miners even like to use this technology?
Miners learn to love using MOSS when marking-up a face underground because of the ease of use and communication from the software – they take pride in seeing the results from their work.
Is quality of work compromised for efficiency?
Quality is a significant factor that MOSS helps to improve with it’s attention to accuracy and efficiency – two critical elements in the mining industry today. Miner’s won’t have to sacrifice time or otherwise, as it makes their job easier and more rewarding. Miners take pride of workmanship when they can see direct results in real-time to compare the markup with the engineer’s design.
Who can use MOSS?
Miners of all skill levels can benefit from MOSS but especially beginners and with a new generation of miners joining the workforce that are used to using technology for every task it is a smooth learning process. A wealth of information is gathered during the markup process which is sent directly to operations, engineering and geology for immediate evaluation, which helps the entire mine.
What if the tripod gets hit /moved?
If the miner hits the tripod, say from tripping over it, MOSS alerts the miner right away about the instrument coming off level and won’t allow you to go forward.